

CAM PROGRAMMING USING AUTODESK POWERMILL

MACHINING STRATEGIES OVERVIEW
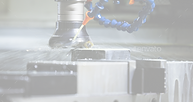
Block Prepare
Block preparation includes deburring the stock and facing or squaring all the sides of the block and make it to the size of the workpiece to be machined. As mentioned, both the block for the core and cavity prepared using curve machining - FACING operation. Facing is done using 4.0D tool for both the block. once the block is prepared then the rest of the machining can be carried out step by step.

Roughing Strategies
Roughing is basically done to remove a huge amount of material from the block. Starting from the largest size tool available to 0.500 dia tipped radius tools. The block can be prepared for semi-finishing operation with up to 0.05"-0.02" material left on the floors and the walls. The general strategy used for roughing is "MODEL AREA CLEARANCE" and "MODEL REST AREA CLEARANCE" with little loose tolerance of 0.002-0.005. Previous stages of the stock model are referenced for each new roughing toolpath with a smaller diameter of the tool. Once the major material from the block is removed with the 0.500D tool, then the block can be stress relieved and prepared for semi-finish operations.

Semi-Finish Strategies
After roughing majority of the semi-finishing operations are performed using tool size from 0.500D to 0.125D or smaller. Some areas can not be machined using flat or tip rad endmills so, a larger size (up to 0.5D) ball nose end-mills are used to perform semi-finishing operations. Leaving 0.01" material on the walls and floor for finishing operations with a tight tolerance of 0.002-0.001. Majority strategies for semi-finish consist of - MODEL REST AREA CLEARANCE, STEEP AND SHALLOW FINISH, OPTIMISED CONSTANT Z, CONSTANT Z, or any other based on the area that needs to be machined.

Finishing Strategies
FInishing is mostly done to maintain high tolerance and surface finish. Ball nose end mills are used for the majority of finishing operations. Only true flat surfaces are machined using endmills or tip rad tools. The rest material from semi-finish is removed using tight tolerance finishing strategies with a very small step-over and step-down and no stock to leave. Finishing has to be done with a very tight tolerance of 0.001-0.0002. The majority of finishing strategies consist of - 3D OFFSET FINISH, PROFILE FINISH, RASTER, CONSTANT Z FINISH, CORNER FINISHING STRATEGIES, SURFACE FINISH, OFF-SET FLAT, and RATHER FLAT.


MACHINING CRITERIA & MASTER TOOLING
Machining has to be done with multiple machines and tooling setups. Roughing is majorly carried out using a VMC with a more rigid setup while semi-finishing and finishing carried out in a 5-axis machine setup for finer surface finish. The stock size for both the part is 29.75"*21.1"*6.4".
The image on the right shows the master tolling list used to machine core and cavity. Tool size bigger than 0.500D is used for roughing with roughing cutting data and standard holder size. Rest tools used for both semi-finish and finishing. As listed the tools have cutting data according to their purpose. All the tip rad and endmill tools have SFM of 1000 and feed/tooth of 0.02 while axial stepover is 3% and radial step over is 70%. Ball nose end mills have SFM less than 800 and feed rate 0.006 while axial stepover is 1% and radial step over is 10%.
